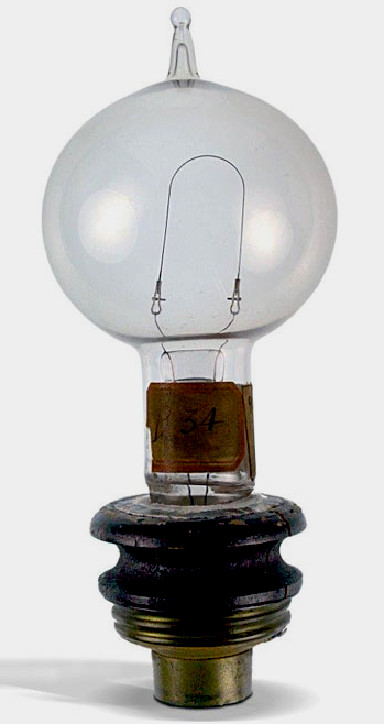
A
selection of Thomas Edison's incandescent lamps, using carbon filament
light bulbs. Antique-style Edison bulbs proliferate in trendy bars and restaurants, most of us know next to nothing about this revolutionary little lamp.
Where
would we be without lighting to be able to see and work at night.
Candles and oil lamps first gave humans the ability to escape the normal
hours of daytime when useful work could be achieved. Imagine how many
books have been written by artificial lighting. Degrees obtained by
studying well into the night. Factories that can operate 24/7. All made
possible by the use of manmade lighting. Let there be light indeed. And
so man gained another advantage over other animals on earth.
It
was the invention of the humble carbon filament, encased in an evacuated
glass
bulb, that heralded electric lighting, to replace gas lamps that were
common at that time. This was by no means perfect, but have a practical
lifetime. And with screw in, or bayonet, quick release fittings,
replacement of blown bulbs was relatively easy, no more fiddly wiring
and risk of shocks. Then, with mass
production, the light bulb became affordable.
Electric
lighting was constant, not liable to be blown out by a gust of wind. So, ideal for street
lighting. And it was safer too. Thus, armies of inventors stove to solve
the problem of finding a material that would glow brightly, when electricity
was passed through it. Three examples of which made the best use of the ideas that had been
developed to that time, by way of amalgamation.
The
perfection of the incandescent light bulb, created a vacuum in the
supply of electricity, the demand for which was consumer led. Everybody
wanted electric lights. But not to run off batteries.
They needed mains electricity, and that meant there was money to be made
in generating this modern service. Something Thomas Edison was keen to
champion. Along with Joseph
Swan, John Hopkinson, and entrepreneurs like
the Baron von Roemer and his son Major Charles de Roemer.
A
modern screw in base, electric light bulb
TWENTY-TWO INVENTORS
Historians Robert Friedel and Paul Israel list 22 inventors of incandescent lamps prior to Joseph Swan and Thomas Edison.
They conclude that Edison's version was able to outstrip the others because of a combination of three factors: an effective incandescent material, a higher vacuum than others were able to achieve (by use of the Sprengel pump) and a high resistance that made power distribution from a centralized source economically viable.
Historian Thomas Hughes has attributed Edison's success to his development of an entire, integrated system of electric lighting.
The lamp was a small component in his system of electric lighting, and no more critical to its effective functioning than the Edison Jumbo generator, the Edison main and feeder, and the parallel-distribution system. Other inventors with generators and incandescent lamps, and with comparable ingenuity and excellence, have long been forgotten because their creators did not preside over their introduction in a system of lighting.
— Thomas P. Hughes, In Technology at the Turning Point, edited by W. B. Pickett
TUNGSTEN FILAMENTS + INERT GAS
On 13 December 1904, Hungarian Sándor Just and Croatian Franjo Hanaman were granted a Hungarian patent (No. 34541) for a tungsten filament lamp that lasted longer and gave brighter light than the carbon filament. Tungsten filament lamps were first marketed by the Hungarian company Tungsram in 1904. This type is often called
Tungsram-bulbs in many European countries. Filling a bulb with an inert gas such as argon or nitrogen slows down the evaporation of the tungsten filament compared to operating it in a vacuum. This allows for greater temperatures and therefore greater efficacy with less reduction in filament life.
In 1906, William D. Coolidge developed a method of making "ductile tungsten" from sintered tungsten which could be made into filaments while working for General Electric Company. By 1911 General Electric had begun selling incandescent light bulbs with ductile tungsten wire.
In 1913, Irving Langmuir found that filling a lamp with inert gas instead of a vacuum resulted in twice the luminous efficacy and reduced bulb blackening.
In 1917, Burnie Lee Benbow was granted a patent for the coiled coil filament, in which a coiled filament is then itself wrapped into a coil by use of a mandrel. In 1921, Junichi Miura created the first double-coil bulb using a coiled coil tungsten filament while working for Hakunetsusha (a predecessor of Toshiba). At the time, machinery to mass-produce coiled coil filaments did not exist. Hakunetsusha developed a method to mass-produce coiled coil filaments by 1936.
Between 1924 and the outbreak of the Second World War, the Phoebus cartel attempted to fix prices and sales quotas for bulb manufacturers outside of North America.
In 1925, Marvin Pipkin, an American chemist, patented a process for frosting the inside of lamp bulbs without weakening them, and in 1947, he patented a process for coating the inside of lamps with silica.
In 1930, Hungarian Imre Bródy filled lamps with krypton gas rather than argon, and designed a process to obtain krypton from air. Production of krypton filled lamps based on his invention started at Ajka in 1937, in a factory co-designed by Polányi and Hungarian-born physicist Egon
Orowan.
By 1964, improvements in efficiency and production of incandescent lamps had reduced the cost of providing a given quantity of light by a factor of thirty, compared with the cost at introduction of Edison's lighting system.
Consumption of incandescent light bulbs grew rapidly in the US. In 1885, an estimated 300,000 general lighting service lamps were sold, all with carbon filaments. When tungsten filaments were introduced, about 50 million lamp sockets existed in the US. In 1914, 88.5 million lamps were used, (only 15% with carbon filaments), and by 1945, annual sales of lamps were 795 million (more than 5 lamps per person per year).
COST AND EFFICIENCY
Prompted by legislation in various countries mandating increased bulb efficiency, "hybrid" incandescent bulbs were introduced by Philips. The
"Halogena Energy Saver" incandescents can produce about 23 lm/W; about 30 percent more efficient than traditional
incandescents, by using a reflective capsule to reflect formerly wasted infrared radiation back to the filament from which it can be re-emitted as visible light. This concept was pioneered by
Duro-Test in 1980 with a commercial product that produced 29.8 lm/W. More advanced reflectors based on interference filters or photonic crystals can theoretically result in higher efficiency, up to a limit of about 270 lm/W (40% of the maximum efficacy possible). Laboratory proof-of-concept experiments have produced as much as 45 lm/W, approaching the efficacy of compact fluorescent bulbs.
The initial cost of an incandescent bulb is small compared to the cost of the energy it uses over its lifetime. Incandescent bulbs have a shorter life than most other lighting, an important factor if replacement is inconvenient or expensive.
Some types of lamp, including incandescent and fluorescent, emit less light as they age; this may be an inconvenience, or may reduce effective lifetime due to lamp replacement before total failure. A comparison of incandescent lamp operating cost with other light sources must include illumination requirements, cost of the lamp and labor cost to replace lamps (taking into account effective lamp lifetime), cost of electricity used, effect of lamp operation on heating and air conditioning systems.
When used for lighting in houses and commercial buildings, the energy lost to heat can significantly increase the energy required by a building's air conditioning system. During the heating season heat produced by the bulbs is not wasted, although in most cases it is more cost effective to obtain heat from the heating system. Regardless, over the course of a year a more efficient lighting system saves energy in nearly all climates.
Since incandescent light bulbs use more energy than alternatives such as CFLs and LED lamps, many governments have introduced measures to ban their use, by setting minimum efficacy standards higher than can be achieved by incandescent lamps.
Measures to ban light bulbs have been implemented in the European Union, the United States, Russia, Brazil, Argentina, Canada and Australia, among others.
In Europe, the EC has calculated that the ban contributes 5 to 10 billion euros to the economy and saves 40 TWh of electricity every year, translating in CO2 emission reductions of 15 million
tonnes.
Objections to banning the use of incandescent light bulbs include the higher initial cost of alternatives and lower quality of light of fluorescent lamps. Some people have concerns about the health effects of fluorescent lamps.
SERIOUS RESEARCH
Thomas Edison began serious research into developing a practical incandescent lamp in 1878. Edison filed his first patent application for "Improvement In Electric Lights" on 14 October 1878. After many experiments, first with carbon in the early 1880s and then with platinum and other metals, in the end Edison returned to a carbon filament.
The first successful test was on 22 October 1879, and lasted 13.5 hours. Edison continued to improve this design and by 4 November 1879, filed for a US patent for an electric lamp using "a carbon filament or strip coiled and connected ... to platina contact wires." Although the patent described several ways of creating the carbon filament including using "cotton and linen thread, wood splints, papers coiled in various ways," Edison and his team later discovered that a carbonized bamboo filament could last more than 1200 hours.
In 1880, the Oregon Railroad and Navigation Company steamer, Columbia, became the first application for Edison's incandescent electric lamps (it was also the first ship to use a dynamo).
COMMERCIAL PRE-HISTORY
In 1761, Ebenezer Kinnersley demonstrated heating a wire to incandescence.
In 1802, Humphry Davy used what he described as "a battery of immense size", consisting of 2,000 cells housed in the basement of the Royal Institution of Great Britain, to create an incandescent light by passing the current through a thin strip of platinum, chosen because the metal had an extremely high melting point. It was not bright enough nor did it last long enough to be practical, but it was the precedent behind the efforts of scores of experimenters over the next 75 years.
Over the first three-quarters of the 19th century, many experimenters worked with various combinations of platinum or iridium wires, carbon rods, and evacuated or semi-evacuated enclosures. Many of these devices were demonstrated and some were patented.
In 1835, James Bowman Lindsay demonstrated a constant electric light at a public meeting in Dundee, Scotland. He stated that he could "read a book at a distance of one and a half feet". However he did not develop the electric light any further.
In 1838, Belgian lithographer Marcellin Jobard invented an incandescent light bulb with a vacuum atmosphere using a carbon filament.
In 1840, British scientist Warren de la Rue enclosed a coiled platinum filament in a vacuum tube and passed an electric current through it. The design was based on the concept that the high melting point of platinum would allow it to operate at high temperatures and that the evacuated chamber would contain fewer gas molecules to react with the platinum, improving its longevity. Although a workable design, the cost of the platinum made it impractical for commercial use.
In 1841, Frederick de Moleyns of England was granted the first patent for an incandescent lamp, with a design using platinum wires contained within a vacuum bulb. He also used carbon.
In 1845, American John W. Starr acquired a patent for his incandescent light bulb using carbon filaments. He died shortly after obtaining the patent, and his invention was never produced commercially.
In 1851, Jean Eugčne Robert-Houdin publicly demonstrated incandescent light bulbs on his estate in
Blois, France. His light bulbs are on display in the museum of the Château de
Blois.
In 1859, Moses G. Farmer built an electric incandescent light bulb using a platinum filament. He later patented a light bulb which was purchased by Thomas Edison.
In 1872, Russian Alexander Lodygin invented an incandescent light bulb and obtained a Russian patent in 1874. He used as a burner two carbon rods of diminished section in a glass receiver, hermetically sealed, and filled with nitrogen, electrically arranged so that the current could be passed to the second carbon when the first had been consumed. Later he lived in the US, changed his name to Alexander de Lodyguine and applied and obtained patents for incandescent lamps having chromium, iridium, rhodium, ruthenium, osmium, molybdenum and tungsten filaments, and a bulb using a molybdenum filament was demonstrated at the world fair of 1900 in Paris.
On 24 July 1874, a Canadian patent was filed by Henry Woodward and Mathew Evans for a lamp consisting of carbon rods mounted in a nitrogen-filled glass cylinder. They were unsuccessful at commercializing their lamp, and sold rights to their patent (U.S. Patent 0,181,613) to Thomas Edison in 1879.
Heinrich Göbel in 1893 claimed he had designed the first incandescent light bulb in 1854, with a thin carbonized bamboo filament of high resistance, platinum lead-in wires in an all-glass envelope, and a high vacuum. Judges of four courts raised doubts about the alleged Göbel anticipation, but there was never a decision in a final hearing due to the expiry date of Edison's patent. A research work published in 2007 concluded that the story of the Göbel lamps in the 1850s was a legend.
Incandescent light bulbs consist of an air-tight glass enclosure (the envelope, or bulb) with a filament of tungsten wire inside the bulb, through which an electric current is passed. Contact wires and a base with two (or more) conductors provide electrical connections to the filament. Incandescent light bulbs usually contain a stem or glass mount anchored to the bulb's base that allows the electrical contacts to run through the envelope without air or gas leaks. Small wires embedded in the stem in turn support the filament and its lead wires.
An electric current heats the filament to typically 2,000 to 3,300 K (1,730 to 3,030 °C; 3,140 to 5,480 °F), well below tungsten's melting point of 3,695 K (3,422 °C; 6,191 °F). Filament temperatures depend on the filament type, shape, size, and amount of current drawn. The heated filament emits light that approximates a continuous spectrum. The useful part of the emitted energy is visible light, but most energy is given off as heat in the near-infrared wavelengths.
GLASS BULBS
Most light bulbs have either clear or coated glass. Coated glass bulbs have kaolin clay blown in and electrostatically deposited on the interior of the bulb. The powder layer diffuses the light from the filament. Pigments may be added to the clay to adjust the color of the light emitted. Kaolin diffused bulbs are used extensively in interior lighting because of their comparatively gentle light. Other kinds of colored bulbs are also made, including the various colors used for "party bulbs", Christmas tree lights and other decorative lighting. These are created by coloring the glass with a
dopant; which is often a metal like cobalt (blue) or chromium (green). Neodymium-containing glass is sometimes used to provide a more natural-appearing light.
The glass bulb of a general service lamp can reach temperatures between 200 and 260 °C (392 and 500 °F). Lamps intended for high power operation or used for heating purposes will have envelopes made of hard glass or fused quartz.
If a light bulb envelope leaks, the hot tungsten filament reacts with air, yielding an aerosol of brown tungsten nitride, brown tungsten dioxide, violet-blue tungsten
pentoxide, and yellow tungsten trioxide that then deposits on the nearby surfaces or the bulb interior.
CARBON FILAMENTS
The first commercially successful light bulb filaments were made from carbonized paper or bamboo. Carbon filaments have a negative temperature coefficient of resistance—as they get hotter, their electrical resistance decreases. This made the lamp sensitive to fluctuations in the power supply, since a small increase of voltage would cause the filament to heat up, reducing its resistance and causing it to draw even more power and heat even further.
In the "flashing" process, carbon filaments were heated by current passing through them while in an evacuated vessel containing hydrocarbon vapor (usually gasoline). The carbon deposited on the filament by this treatment improved the uniformity and strength of filaments as well as their efficiency. A metallized or
"graphitized" filament was first heated in a high-temperature oven before flashing and lamp assembly. This transformed the carbon into graphite, which further strengthened and smoothed the filament. This also changed the filament to have a positive temperature coefficient, like a metallic conductor, and helped stabilize the lamp's power consumption, temperature and light output against minor variations in supply voltage.
TANTALUM FILAMENTS
In 1902, the Siemens company developed a tantalum lamp filament. These lamps were more efficient than even graphitized carbon filaments and could operate at higher temperatures. Since tantalum metal has a lower resistivity than carbon, the tantalum lamp filament was quite long and required multiple internal supports. The metal filament had the property of gradually shortening in use; the filaments were installed with large loops that tightened in use. This made lamps in use for several hundred hours quite fragile. Metal filaments had the property of breaking and re-welding, though this would usually decrease resistance and shorten the life of the filament. General Electric bought the rights to use tantalum filaments and produced them in the US until 1913.
From 1898 to around 1905, osmium was also used as a lamp filament in Europe. The metal was so expensive that used broken lamps could be returned for partial credit. It could not be made for 110 V or 220 V so several lamps were wired in series for use on standard voltage circuits.
TUNGSTEN FILAMENTS
In 1904, the tungsten filament was developed by Croatian inventors Franjo Hanaman and Alexander Just. Tungsten metal was initially not available in a form that allowed it to be drawn into fine wires. Filaments made from sintered tungsten powder were quite fragile. By 1910, a process was developed by William D. Coolidge at General Electric for production of a ductile form of tungsten. The process required pressing tungsten powder into bars, then several steps of sintering, swaging, and then wire drawing. It was found that very pure tungsten formed filaments that sagged in use, and that a very small "doping" treatment with potassium, silicon, and aluminium oxides at the level of a few hundred parts per million greatly improved the life and durability of the tungsten filaments.
To improve the efficiency of the lamp, the filament usually consists of multiple coils of coiled fine wire, also known as a 'coiled coil'. Light bulbs using coiled coil filaments are sometimes referred to as 'double-coil bulbs'. For a 60-watt 120-volt lamp, the uncoiled length of the tungsten filament is usually 580 millimetres (22.8 in), and the filament diameter is 0.046 millimetres (0.0018 in).
The advantage of the coiled coil is that evaporation of the tungsten filament is at the rate of a tungsten cylinder having a diameter equal to that of the coiled coil. The coiled-coil filament evaporates more slowly than a straight filament of the same surface area and light-emitting power. As a result, the filament can then run hotter, which results in a more efficient light source while lasting longer than a straight filament at the same temperature.
Alice Vanderbilt, electric light costume
LIGHT
EMITTING DIODES: LEDS
After
all manner of brighter lamps, mainly for automobiles, longer lasting
tungsten filament, halogen and xenon bulbs, were finally ousted by LEDs.
The advantage of light emitting diodes being that they produce more
light for less energy, and last around 25,000 hours, or three years of
constant use. Whereas most drivers would only use for 2-4 hours a day
average. Meaning that LED lights will last for about 17 years; longer
than the life of most vehicles.
LED
lighting has drastically cut the lighting cost of houses and factories,
reducing the energy requirement of every country, provided that their
population take to the technology.
A
hive of local activity, in the Sussex backwater of Herstmonceux. The
driver from all of this was electric lighting, to replace candles and
gas lighting.
The
machinery at Herstmonceux Generating Works was gas powered in its final
guise. The gas coming from the pyrolysis of coal. Hence, the sizeable brick built
bunker, convenient to shed number three, where the gas making plant
was installed. The complex is interesting, unique, because it not only generated
electricity, but stored it in Shed number One, a room filled with large lead-acid
accumulator batteries housed in sizeable glass containers, with sufficient
energy storage capacity to provide electric
lighting and cooking overnight, to the village before 1913, as confirmed in the operating
instructions from 1911.
CHAPTERS
The Industrial
Revolution
|
|
Electricity and Magnetism
- Electric
Lighting Acts 1882 - 1909
|
|
Let there be light,
glass bulbs to LEDs
|
|
Public supply
|
|
Rural supply
|
|
Lime Park
|
|
Generating station 1982/3
|
|
Generating station – Power House,
36 hp National Gas engine
|
|
Honeysett
Brothers - Electric Bakers & Confectioners, Gardner Street
|
|
Flour
from the millers at Windmill Hill (Trust), tallest post
windmill, UK
|
|
Archaeology – Machinery
|
|
Archaeology – Boiler Room
|
|
Archaeology – Batteries
|
|
Stabling,
horses, carriages & blacksmiths - The Old Rectory
- conversion
|
|
Sussex Express & Kent Mail Oct 1913
- cooking demonstrations
|
|
Coal deliveries &
plan of building
|
|
Map of Herstmonceux
|
|
The Sussex Industrial Archaeology Society
|
|
The County Archaeologist
|
|
The chauffeur’s daughter
|
|
The engineer’s son
|
|
The Department for Culture Media & Sport
(DCMS)
|
|
English Heritage & Monument
At Risk Protection Programmes MARS
|
|
Sussex Express
December 1999
|
|
Archaeology South
East, London University, Survey & Report 1999
|
|
Generating Works -
Instructions 1911
|
|
Amberley
Museum, Arundel, West Sussex
|
|
The rise of
renewables & climate cooling
|
|
UNESCO World Heritage Convention
|
|
Site
Restoration and Development Proposals - Phases - 3D
VR
|
ONE -
TWO -
THREE -
FOUR - FIVE |
If
you know of any information that may help us complete this story, please get in
touch.
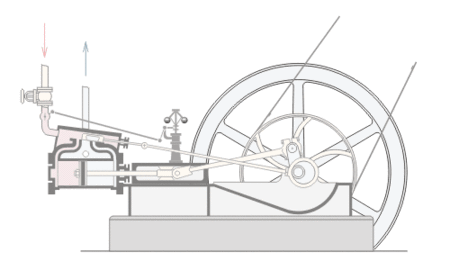
|